CNC Machining: Empowering the Metal Fabrication Industry
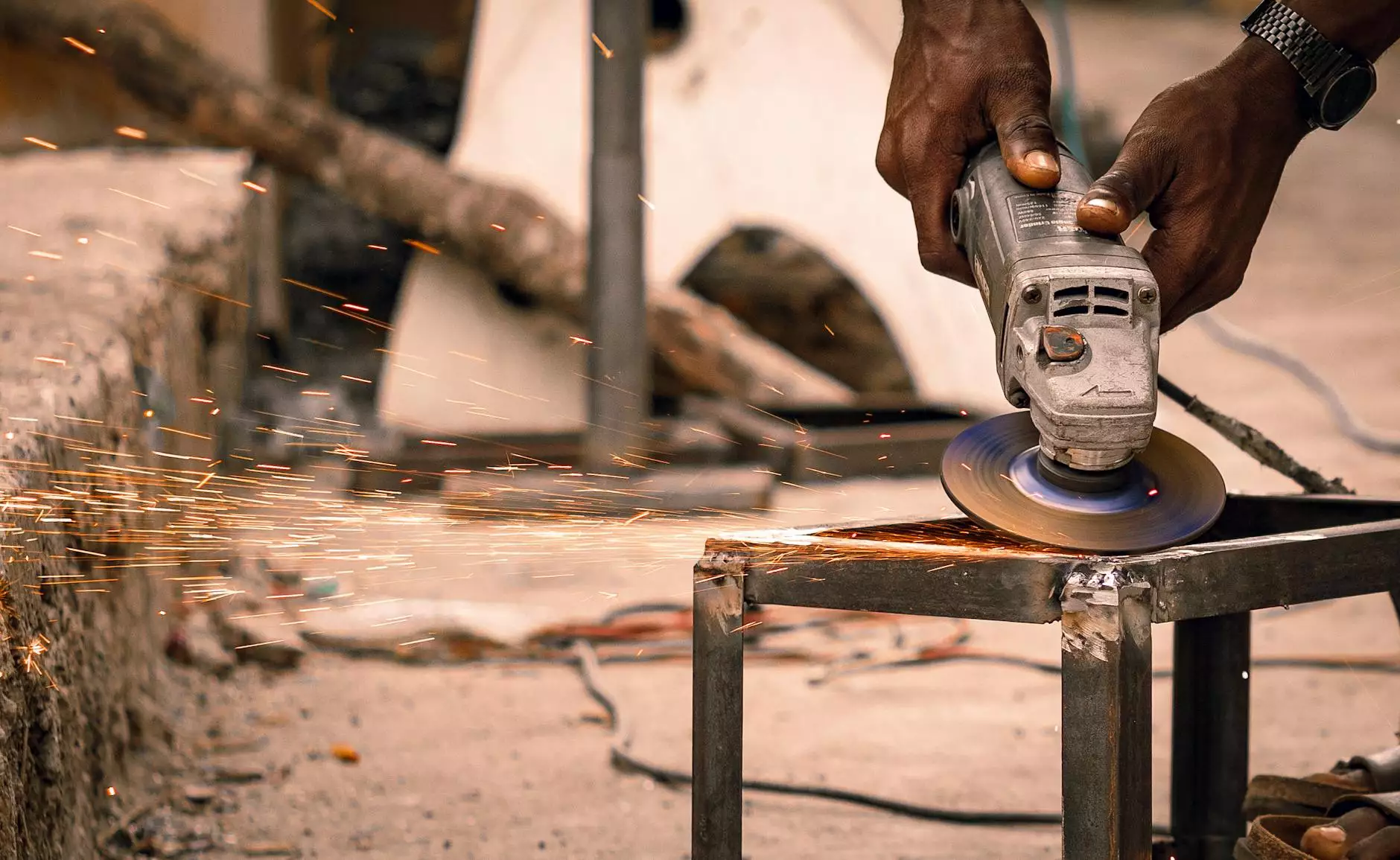
Understanding CNC Machining
CNC machining stands for Computer Numerical Control machining, a process that uses computer software to control machine tools. This technology enables us to create intricate designs with a remarkable degree of precision and accuracy. With the ability to automate the milling, turning, and drilling processes, CNC machining has become an invaluable asset in the field of metal fabrication.
The Importance of CNC Machining in Metal Fabrication
In today's competitive landscape, companies in the metal fabrication industry are increasingly turning to cnc machining to meet growing demands for high-quality parts. The reasons for this shift are numerous:
- Increased Precision: CNC machines can achieve tolerances of 0.001 inches or less, ensuring that each part is manufactured to the highest standards.
- Higher Efficiency: The automation aspect of CNC machining increases production speed and reduces human error, leading to faster turnaround times.
- Cost Effectiveness: Despite the initial investment in technology, CNC machining reduces waste and labor costs, which results in significant savings over time.
- Flexibility: CNC machines can be easily reprogrammed to handle different tasks, allowing for quick changes in production lines as market needs shift.
Applications of CNC Machining in Various Industries
The versatility of cnc machining opens up opportunities across various sectors, including:
Aerospace Industry
CNC machining is pivotal in manufacturing components for aircraft and spacecraft, where precision and reliability are non-negotiable. Parts such as brackets, frames, and engine components benefit immensely from CNC technology.
Automotive Industry
In the automotive sector, cnc machining is utilized for producing intricate engine parts, transmission housings, and custom components. This technology not only speeds up production but also enhances the safety and performance of the vehicles.
Medical Devices
The medical field demands the highest accuracy for the production of surgical instruments and implants. CNC machining provides the precision required, ensuring that such devices meet strict regulations and standards.
Electronics
From enclosures to custom connectors, the electronics industry uses CNC machining to produce highly detailed parts that are essential for electronic devices to function effectively.
Key Advantages of CNC Machining for Metal Fabricators
Metal fabricators like DeepMould.net recognize several key advantages when incorporating cnc machining into their operations:
- Enhanced Productivity: CNC machines can operate continuously, performing multiple tasks that would require multiple setups for manual machines.
- Reduced Lead Times: With the ability to quickly produce high volumes of parts, businesses can respond faster to market demands.
- Improved Quality Control: The automation and precision of CNC machining facilitate rigorous quality checks, resulting in consistent product quality.
- Intricate Design Capabilities: Complex geometries and designs that would be nearly impossible with manual methods can be readily achieved through CNC machining.
How CNC Machining Works
CNC machining involves several steps to transform raw materials into finished products:
- Design: Using CAD software, engineers or designers create a detailed 3D model of the part to be manufactured.
- Programming: The CAD model is converted into G-code, the language that CNC machines understand. This includes instructions on how to move the machine and what tools to use.
- Setup: The raw material is secured to the machine bed, and the appropriate tools are loaded into the CNC machine.
- Machining: The CNC machine follows the programmed instructions to cut, shape, or form the metal material into the desired part.
- Finishing: Once the machining is complete, additional processes like sanding, polishing, or coating may be applied to achieve the final specifications.
Choosing the Right CNC Machining Provider
Selecting the right provider for cnc machining is crucial for ensuring a smooth manufacturing process and high-quality outcomes. Here are some tips to consider:
- Experience: Look for a company with a solid track record in CNC machining, particularly in your industry.
- Capabilities: Ensure the provider has the necessary equipment and technology to handle your specific needs and materials.
- Quality Assurance: Choose a provider with stringent quality control processes to ensure your parts meet specifications.
- Customer Service: A responsive and knowledgeable customer service team can greatly enhance your experience when working with a CNC machining provider.
Future Trends in CNC Machining for Metal Fabrication
The world of CNC machining is evolving rapidly. Here are some trends shaping its future:
Automation and AI
The incorporation of artificial intelligence in CNC machines can lead to smarter manufacturing processes, predictive maintenance, and enhanced production capabilities, allowing companies to optimize operations further.
3D Printing Integration
Combining CNC machining with 3D printing allows for the creation of parts that are not only strong and lightweight but also feature complex designs not achievable through traditional methods.
Eco-Friendly Manufacturing
As sustainability becomes a priority across industries, the focus on creating eco-friendly CNC machining processes is likely to increase. This includes reducing waste, using recyclable materials, and improving energy efficiency.
Final Thoughts
In conclusion, cnc machining stands at the forefront of the metal fabrication industry, offering unparalleled precision, efficiency, and flexibility. For businesses like DeepMould.net, embracing this technology means better product quality, reduced lead times, and an edge over competitors. As the industry continues to evolve, staying informed about trends and advancements in CNC machining will be critical for success in the ever-changing landscape of metal fabrication.
As we look to the future, it is clear that the advancements in CNC machining will serve not just as a tool for manufacturing but as a catalyst for innovation across various sectors. Embracing this technology today ensures a prosperous tomorrow for businesses that work with metal fabricators.